How to Achieve Predictive Maintenance with IoT? 4Geeks Shows You How
Unlock the power of predictive maintenance with IoT! By leveraging real-time data, AI, and sensors, businesses can reduce downtime, cut costs, and boost efficiency. Learn how 4Geeks’ end-to-end IoT solutions help predict failures, optimize operations, and future-proof your assets.
In today’s competitive industrial landscape, predictive maintenance is revolutionizing how businesses manage equipment and operations. By predicting equipment failures before they happen, organizations can reduce downtime, improve asset efficiency, and lower maintenance costs.
The key enabler of predictive maintenance is the Internet of Things (IoT), which allows businesses to collect, monitor, and analyze machine data in real-time. In this blog, we’ll explore how IoT makes predictive maintenance possible and how 4Geeks can help organizations implement this game-changing strategy effectively.
What is Predictive Maintenance?
Predictive maintenance is a strategy that leverages data analytics and sensors to forecast when equipment is likely to fail or degrade. Unlike reactive maintenance (where issues are resolved only after failure) and preventive maintenance (where maintenance is scheduled periodically regardless of condition), predictive maintenance relies on real-time monitoring to ensure equipment is serviced only when needed. This approach minimizes downtime and extends asset lifespan.
The adoption of IoT technology brings predictive maintenance to a new level by enabling continuous tracking of asset performance through sensors, cloud computing, and AI-based analytics. This ensures maintenance is planned proactively—based on evidence from machine health, rather than assumptions or fixed schedules.
Key Benefits of Predictive Maintenance with IoT
Data collected by IoT-powered predictive maintenance systems helps businesses achieve multiple benefits:
- Reduced Downtime: Predictive alerts ensure that machines are maintained before breakdowns occur, minimizing unplanned stoppages.
- Lower Maintenance Costs: Timely servicing avoids unnecessary repairs and extends the lifespan of parts, reducing replacement expenses by up to 40%.
- Optimized Spare Part Management: Knowing which components are prone to failure allows businesses to optimize their spare part inventory.
- Increased Operational Efficiency: Properly maintained equipment performs more efficiently, leading to higher productivity and reduced energy consumption.
- Longer Asset Lifespan: Regular insights from IoT sensors ensure equipment is not over-maintained, preventing wear from unnecessary interventions.
How IoT Enables Predictive Maintenance
IoT technology plays a pivotal role in predictive maintenance by automating the data collection and analysis process. Here’s how the IoT ecosystem supports predictive maintenance:
- Sensor Deployment: Sensors such as temperature, vibration, pressure, humidity, and ultrasonic sensors are attached to equipment to gather performance data.
- Data Transmission via IoT Gateways: The collected data is transmitted to cloud platforms through IoT gateways in real-time, enabling remote monitoring.
- Data Storage and Processing in the Cloud: The cloud stores and processes massive datasets using AI and machine learning models. This allows systems to recognize patterns that indicate potential failures.
- Predictive Alerts and Insights: IoT platforms generate alerts when they detect anomalies, ensuring maintenance teams receive notifications early enough to intervene.
- Integration with Enterprise Systems: The data from IoT systems can be integrated with ERP or CMMS (Computerized Maintenance Management Systems) to streamline the maintenance workflow.
For example, vibration sensors on a motor can detect unusual vibrations that signal bearing wear. With enough data, the system learns to predict when the motor will need replacement, ensuring the maintenance team receives an alert before failure occurs.
Real-World Use Cases of IoT-Based Predictive Maintenance
1. Automotive Manufacturing:
In automotive production lines, even a few minutes of downtime can cost thousands of dollars. IoT-based predictive maintenance helps manufacturers continuously monitor key machinery like assembly robots and conveyor belts. When a robotic arm shows early signs of wear, such as abnormal speed reductions or erratic movement, sensors send an alert, allowing the team to service it without disrupting production.
Outcome:
- 30% reduction in downtime
- 20% savings in spare part procurement
- Increased production efficiency
2. Oil and Gas Industry:
Oil rigs and pipelines operate in harsh environments where equipment failure can lead to disastrous outcomes. With IoT sensors installed on pumps, compressors, and valves, companies collect pressure and flow data remotely. Machine learning models analyze the data to predict failures in advance, preventing catastrophic breakdowns.
Outcome:
- 25% increase in equipment uptime
- Reduced risk of environmental hazards
- 15% lower maintenance costs
3. Smart Buildings and HVAC Systems:
In large commercial buildings, HVAC (heating, ventilation, and air conditioning) systems consume a significant amount of energy. Predictive maintenance powered by IoT sensors ensures the system runs at peak efficiency by detecting blockages, refrigerant leaks, or motor failures early. With real-time monitoring, building managers can address potential issues before tenants are impacted.
Outcome:
- 20% energy savings
- Improved tenant comfort and satisfaction
- 35% reduction in HVAC maintenance costs
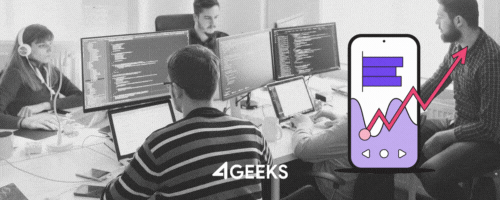
Custom Software Development Services
Work with our in-house Project Managers, Software Engineers and QA Testers to build your new custom software product or to support your current workflow, following Agile, DevOps and Lean methodologies.
Implementing Predictive Maintenance with 4Geeks
4Geeks specializes in helping businesses harness IoT to build scalable predictive maintenance solutions. Here’s how we can assist organizations in implementing predictive maintenance efficiently:
- Customized IoT Solution Design: We assess the equipment, identify key performance indicators (KPIs), and design a sensor network tailored to your needs.
- Seamless Data Integration: Our team integrates IoT data with cloud platforms, ERPs, and existing maintenance management systems to provide a holistic view of machine health.
- AI-Powered Analytics: We implement AI and machine learning models that learn from historical data to detect patterns and predict failures with high accuracy.
- Cloud-Based Dashboards: 4Geeks provides intuitive dashboards that give real-time insights into equipment health, enabling proactive decision-making.
- Scalable IoT Solutions: Our systems are designed to scale as your business grows, ensuring predictive maintenance remains effective across all operations.
For example, in a recent project, 4Geeks partnered with a manufacturing company to deploy IoT sensors on its production line. Our predictive maintenance solution resulted in a 28% reduction in downtime and saved the client over $200,000 in maintenance costs within the first year.
Data-Driven Impact: Why Predictive Maintenance is Worth the Investment
Several reports highlight the financial and operational impact of predictive maintenance:
- Deloitte estimates that predictive maintenance can reduce unplanned downtime by 30-50% across industries.
- GE Digital found that predictive analytics can improve equipment lifespan by 20% and reduce maintenance costs by 25%.
- PwC reports that predictive maintenance can deliver up to a 545% return on investment (ROI) over five years.
With real-time monitoring and AI-driven predictions, companies gain the ability to schedule maintenance precisely when needed, eliminating unnecessary interventions and optimizing equipment availability.
Conclusion
The combination of IoT, AI, and cloud technology is transforming maintenance strategies, enabling businesses to predict and prevent equipment failures effectively. Predictive maintenance is no longer a luxury but a necessity in industries where unplanned downtime can have significant financial and operational repercussions.
With benefits like reduced downtime, cost savings, and improved operational efficiency, predictive maintenance powered by IoT represents the future of asset management.
4Geeks is at the forefront of IoT-enabled predictive maintenance, offering businesses the tools and expertise to implement these solutions at scale. From sensor deployment to AI-based analytics and cloud integration, we provide end-to-end IoT solutions designed to meet the unique needs of each business. Whether you're in manufacturing, oil and gas, or facilities management, 4Geeks can help you achieve predictive maintenance success and unlock the full potential of your operations.
By embracing IoT-based predictive maintenance with 4Geeks, organizations not only reduce costs and improve efficiency but also future-proof their operations against unexpected disruptions. The time to act is now—partner with 4Geeks and take the first step toward a smarter, more reliable future.
FAQs
What is predictive maintenance?
Predictive maintenance is a strategy that uses data analytics and sensors to forecast when equipment is likely to fail. Unlike reactive maintenance (fixing issues after they occur) and preventive maintenance (scheduled maintenance regardless of condition), predictive maintenance relies on real-time data to service equipment only when needed. This minimizes downtime and extends the lifespan of your assets.
How does the Internet of Things (IoT) enhance predictive maintenance?
IoT takes predictive maintenance to the next level by enabling continuous asset performance tracking. Sensors collect data, IoT gateways transmit it to the cloud, and AI-powered analytics identify patterns that indicate potential failures. This allows for proactive maintenance based on actual machine health rather than assumptions.
What industries can benefit most from predictive maintenance?
Any industry relying on critical equipment can benefit. This includes manufacturing, oil and gas, transportation, energy, utilities, and building management. Essentially, if downtime is costly or poses safety risks, predictive maintenance offers substantial advantages.
How can I get started with predictive maintenance for my business?
Partnering with an experienced IoT solutions provider like 4Geeks is a crucial first step. They can guide you through the process, from assessing your needs to designing, implementing, and scaling a solution tailored to your specific requirements.